Inspection Robots
Running projects
PILOTs for robotic INspection and maintenance Grounded on advanced intelligent platforms and prototype applications
Funded under H2020 ICT-09-2019-2020 – Robotics in Application Areas
PILOTING project aims to develop a complete inspection platform that will provide to the end-users with the exact and proper information required to plan the necessary maintenance of the infrastructure during its whole lifetime, preventing future accidents and fulfilling the required regulation and industrial standards. Therefore, PILOTING will not be only focused on the development of advanced robotic systems, but also in the development and demonstration of software tools that will allow to properly exploit the information gathered by the robotic vehicles and presenting this information to the end-user (industrial reporting) in order to allow them to make the best decisions to optimize the use of the infrastructures, with the added benefits to the European citizens and the environment.
For more detailed information visit: external page piloting-project.eu/
Completed projects

Fast climbing robots for environments made out of thin metal sheets
The original purpose of this project was the inspection of gas tanks in oversea ships. These expensive tanks have to be inspected regularly for leaks. For doing this, helium gas in inserted from the back and a sniffer probe has to be carried to every point in the tank to find the leaks. The current method using a tethered blimp was too slow and imprecise. Thus, the goal was to access these areas with climbing robots that attach to the surface. Using a state-of-the-art climbing robot was not possible due to the following restrictions:
- Low allowed mass, need for high speed --> suction cups are not possible, magnetic wheels seem the only promising solution
- Thin sheet material --> the magnetic force is limited by saturation in the ground
- Difficult obstacles --> need for mechanisms to carry the wheels over the obstacles
We now developed a new inspection system that can solve all the challenges in this application. The main innovative ideas within this system are:
- separation into two robots: A big robot with high obstacle-passing capabilities carries a second one over the obstacles. This second robot is very simple, lightweight and fast and can drive on the fragile surfaces.
- magnetic wheels that are specially optimized for thin surfaces
- active structure that allows for passing ridge-type obstacles
The actual results are a detailed robot design for the whole system and prototype of the small robot, but the project is in standby for the moment.
Publications:
Fischer, W., Tâche, F. and Siegwart, R. (2007) Inspection System for Very Thin and Fragile Surfaces, Based on a Pair of Wall Climbing Robots with Magnetic Wheels. In Proceedings of the IEEE/RSJ International Conference on Intelligent Robots and Systems. [IROS'2007]
Fischer, W., Tâche, F. and Siegwart, R. (2007) Magnetic Wall Climbing Robot for Thin Surfaces with Specific Obstacles. In Proceedings of the 6th International Conference on Field and Service Robotics. [FSR'07]
The research was funded by
GAZTRANSPORT & TECHNIGAZ, 1, route de Versailles, 78470 Saint-Rémy-lès-Chevreuse, FRANCE, A. Charoy and A. Mangé.
Large Microphone Array
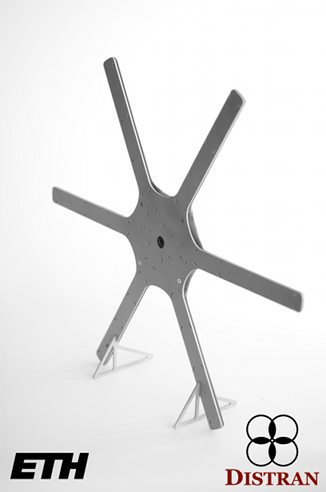
Humans are able, to a certain extent, to determine the location of a sound source and to use this information to focus on a person speech while ignoring the ambient noise.
Similarly, microphones arrays enable to locate sounds and filter them depending of their incoming direction. Unlike light, that propagates too fast to record travel times easily, time difference of arrival (TDOA) of a same sound recorded by two different microphones can be computed directly and used to detect the origin of a sound.Though microphone arrays are known since the 20s for military applications (aircraft detection, artillery localization), the tremendous increase in computational power as well as the miniaturization of microphones have opened new theories and algorithms – precise sound source localization through deconvolution, ambient noise filtering – and new areas of uses: sound filtering in telecommunications (laptops, smart-phones), industrial applications (optimization of airplanes design to reduce noise emission).
Meanwhile, widely spread arrays are nowadays limited to 2, 3 or 4 microphones and are unable to deal with complex situations like multiple speakers, room reverberation or diffraction due to large wavelength of audible sound waves.
In this project, a microphone array with a large number of elements has been built together with a fast middleware architecture that is able to record and stream sounds from 64 sources with low latency. Together with a standard optical camera, the array is able to compute an acoustic image of a scene and to superpose it with the optical image, in real-time.
More information on external page www.distran.ch
This project is supported by a Pioneer Fellowship.
Magnebike: Compact Magnetic Wheeled Inspection Robot with High Mobility
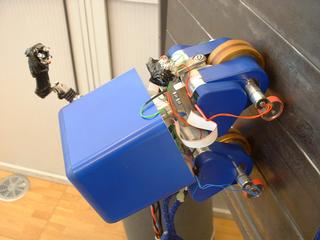
Download Poster 2009 (PDF, 984 KB)
Download Poster 2008 (PDF, 2.3 MB)
Download Poster 2006 (PDF, 1.7 MB)
Characteristics:
- Size (LxWxH) 180x130x120mm
- Mass 3.5kg
- Wheel diameter 60mm
- Magnetic wheel force 250N
- Max. speed 2.7m/min
- Operating voltage 24V
Motivation and goal
Inspection of complex environment with compact mobile robots
- Wide range of inner diameters: it varies from 200mm (max. robot space envelope) up to 700mm.
- Local abrupt inner diameter changes, up to 50mm: 90° convex or concave obstacles.
- Complex arrangement and sequence of the obstacles: triple step or gap.
- Any inclination can be encountered: climbing ability is required.
- Maneuver about in narrow locations and travel on circumferential paths.

Goal: design a mobile robot able to bring inspection sensors in this specific environment
- Locomotion concept: design a compact climbing robot with high mobility.
- Localization strategy: find appropriate sensors (embedded) and implement localization algorithms (external computer) that provide the robot location in the closed environment.
- Integration: the system has to embed low level control electronic and sensors (for the locomotion system control and localization).
Locomotion Concept and Robot Design
- Two wheels in a motorbike arrangement: better adaptation to the surface (flat or curved).
- Magnetic wheel unit including lateral lifter/stabilizer arms. The lifter functionality helps to pass over step obstacles. The stabilizer functionality allows to drive sideway.
- Five active DoF: front/rear wheel, front/rear lifter, steering unit.





Localization and Mapping Concept
SLAM approach
- 3D scan: provides a 3D vizualisation to the user who remote controls the robot.
- Odometry: used to track the robot position between 2 consecutive 3D scans. Used as prior knowledge for the scan matching.
- Scan matching: determines the 3D transformation matrix between 2 consecutive 3D scans, but also to generate a 3D model of the environment.
Sensors
- 3D range finder (rotating Hokuyo-URG04LX)
- 3-axis accelerometer
- Wheel encoders: odometry
- Strain gage between wheel units: to control the wheel speeds (avoid robot deformation)
- Strain gages on lifter arms: to control the lateral stablization system



Algorithm: 3D scan matching
- Scan mathing using ICP (Iteravite Closest Point)



Publications about this work:
PhD thesis
Fabien Tâche (2010) Robot Locomotion and Localization on 3D Complex Shaped Structures. ETHZ.
Journal paper
Fabien Tâche, Wolfgang Fischer, Gilles Caprari, Roland Siegwart, Roland Moser, Francesco Mondada (2009) Magnebike: A Magnetic Wheeled Robot with High Mobility for Inspecting Complex Shaped Structures. Journal of Field Robotics, 26:453–476, May 2009.
Fabien Tâche, François Pomerleau, Michael Bosse, Gilles Caprari, Roland Siegwart, Roland Moser (2010) 3D Localization for the Magnebike Inspection Robot. Submitted to Journal of Field Robotics (May 2010).
Peer-reviewed Proceedings
Fabien Tâche, Wolfgang Fischer, Roland Siegwart, Roland Moser, Francesco Mondada (2007) Compact Magnetic Wheeled Robot With High Mobility for Inspecting Complex Shaped Pipe Structures. In Proceedings of the IEEE/RSJ International Conference on Intelligent Robots and Systems, October 29 - November 2, San Diego, California, USA
Fabien Tâche, Wolfgang Fischer, Roland Moser, Francesco Mondada, Roland Siegwart (2007) Adapted Magnetic Wheel Unit for Compact Robots Inspecting Complex Shaped Pipe Structures. In Proceedings of the IEEE/ASME International Conference on Advanced Intelligent Mechatronics, September 4-7, Zürich, Switzerland
Andreas Breitenmoser, Fabien Tâche, Gilles Caprari, Roland Moser, Roland Siegwart (2010) MagneBike - Toward Multi Climbing Robots for Power Plant Inspection. In Proceedings of the International Conference on Autonomous Agents and Multiagent Systems, May 10 - 14, Toronto, Canada
Frédéric Rochat, Patrick Schoeneich, Fabien Tâche, Francesco Mondada, Hannes Bleuler (2010) Magnetic Wheels Optimization and Application to the MagneBike Climbing Robot. In Proceedings of the International Conference on Climbing and Walking Robots, August 31 - September 3, Nagoya, Japan